特斯拉正逐渐转向一项名为 “unbox(拆箱式)” 新组装工艺。与传统产线的流水线作业方式不同,这一新工艺更类似 “组装乐高积木”:汽车车身无需像以前一样在一条传送带上传送依次组装零部件,特斯拉计划在工厂的专用区域同时组装车辆的不同部分,最后将这些大型子组件装配在一起。与同等产量的传统汽车工厂相比,这项新工艺有望使生产成本减半,制造所需占地面积则减少 40% 以上。
Tesla is gradually transitioning to a new assembly process called “unbox.” Unlike traditional assembly lines, this new process is more akin to “assembling LEGO blocks.” Instead of sequentially moving car bodies along a conveyor belt for component installation, Tesla plans to simultaneously assemble different parts of the vehicles in dedicated areas of the factory. Finally, these large subassemblies will be put together. Compared to traditional car factories with similar output, this new process is expected to reduce production costs by half and require over 40% less floor space.
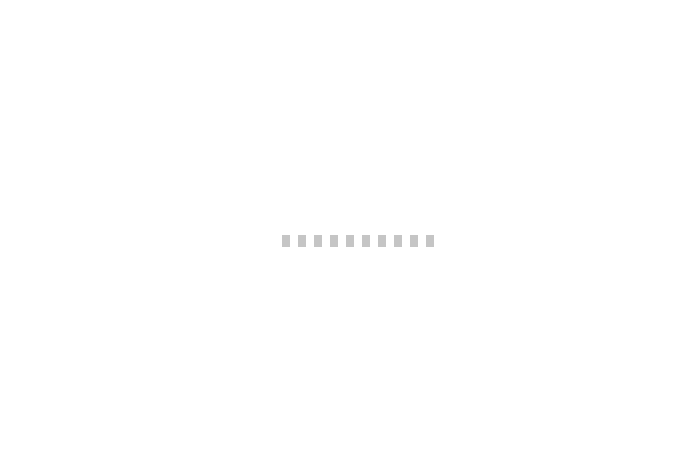